ODM Forging Parts PED4.3 AD2000 Closed Die Forged Steel
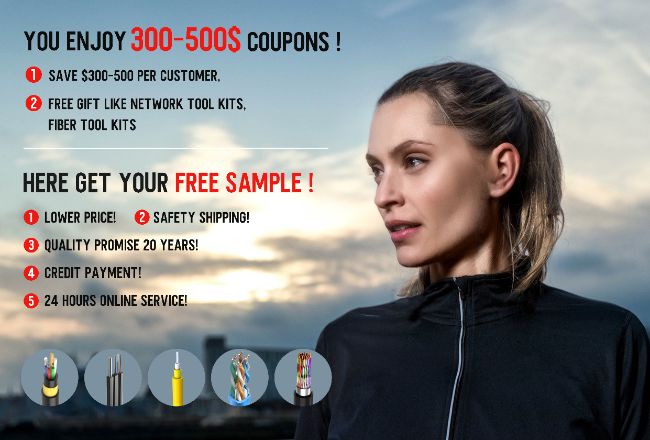
Contact me for free samples and coupons.
Whatsapp:0086 18588475571
Wechat: 0086 18588475571
Skype: sales10@aixton.com
If you have any concern, we provide 24-hour online help.
xMaterial | Stainless Steel;aluminum;steel;etc | Dimensions | Customized Size,according To Drawings |
---|---|---|---|
Application | Industry,Machinery Parts,Auto Parts,agricultural Machinery | Process | Forging,hot Forged,Forging+Rough Machining+Heat Treatment+Final Machining+Inspection |
Surface Treatment | Powder Coating,According To Demand,Zinc Plating,Dacromat Coating,electrophoresis | Product Name | Stainless Steel Close Die Forging Custom Forging Engineering & Design Solutions |
Service | OEM & ODM | Standard | ASTM. AISI. DIN. BS. JIS. NF. AS. AAR |
Certification | PED4.3 AD2000,EN10204-3.1 | Size | Change From 5-2000,Customer's Drawing |
Surface | Plating,Heat Treatment | Tolerance | DIN7526-F,+/-0.01mm |
Usage | Various Usage | Inspection | 100%,Mechinical Property Inspection |
Highlight | AD2000 Forging Parts,Forging Parts PED4.3,AD2000 Closed Die Forged Steel |
Stainless Steel Close Die Forging Custom Forging Engineering & Design Solutions
What Is Closed-Die Forging?
Closed-die forging, or impression-die forging, involves metal being placed between one or more custom-shaped dies. The metal is hammered or pressed, causing it to flow and fill the shaped-die cavities.
Closed-die forging is one of the most commonly used methods for forging steel parts. This process works with the metal’s internal grain structure and can produce stronger, longer-lasting products.
Little to no machining is needed for closed-die forgings. The process simply utilizes the force from a closed-die forging hammer or press, and heat, to deform the metal to fill the die impression or mold.
THE ADVANTAGE OF FLASH IN CLOSED-DIE FORGING
Where both die forgings can result in a thin layer of flash (excess material squeezed out during the die forging process) the closed-die process uses the flash to its advantage. As the flash promptly cools, it increases pressure on the impression, which encourages the metal flash to flow into details/crevices. The excess flash is then manually removed.
CLOSED-DIE FORGING PROS
Better surface finish and superior mechanical properties
Reduced or no machining
Cost-effective for large production runs
Dimensions with tighter tolerances and various shapes can be achieved
More precise, consistent impressions
Ability to reproduce nearly any shape and/or size
CLOSED-DIE FORGING CONS
Not typically economical for short or small production runs due to the cost of die production
Higher setup cost due to costly machines and furnaces
A variety of different processes and technologies are used in forging due the wide variety of formed shapes to be produced. With a comprehensive range of especially developed line concepts from DM we will find the most economical solution for you that meets all the demands for cold, warm, and hot forming as well as precision forging.
DRACHMA (ZHANGJIAGANG) MATERIAL CO.LTD has two main production plants. Zhangjiagang plant is responsible for the rough forming of workpieces, mainly forging process; While Hangzhou plant is mainly responsible for precision machining, welding and inspection of products. We implement this layout mainly to use the industrial advantages of each region to achieve maximum economic benefits.
Traditional processing enterprises often do not have such ability, the lack of blank forming ability is unable to achieve the optimal use of materials, resulting in excessive processing allowance, long cycle, high cost. Zhangjiagang is located in the southern jiangsu province, which has the strongest forging capacity in China. It has a good supporting industry and can realize the diversified production of forging and pressing blanks. Thanks to this, the product cycle of our company is faster, the cost performance is higher, and the forging products have better mechanical properties than the products directly processed by rod or plate.
In addition, our company has strong welding ability, which can weld and assemble parts to achieve system delivery. We adopt the mode of automatic robot welding and manual precision welding to achieve flexibility and high quality.
Name | Type | Quantity | Processing range | Precision(um) |
CNC | MAZAK(QTN350L) | 1 | φ720*1250 | 3 |
CNC | MAZAK(QTN250L) | 1 | φ580*1500 | 3 |
Turn milling center | MAZAK(QTN250M) | 2 | φ580*600 | 3 |
CNC | Newway(NL-634SC) | 1 | φ630*1000 | 5 |
CNC | FUJI(TN-36) | 2 | φ350*290 | 3 |
CNC | HAAS SL30 | 1 | φ620*750 | 3 |
CNC | MAZAK FJV200 | 1 | 560X*410Y*560Z | 3 |
CNC | LGMAZAK NEXUS160AN-2PC | 1 | 560X*410Y*660Z | 10 |
CNC | WHEELEL | 2 | 560X*410Y*660Z | 5 |
Welding | Miller | 1 |
Stainless steel :304/1.4307 316/1.4404 321/1.4541 316Ti/1.4571 317L 904L F44 NO6625 UNS718
440A/B/C 431 446 F6a
Carbon Steel:A105, SA350 LF1, LF2, LF3, LF6, A707, A694, 4130, 4140, 8620, 8630, A182F5, F11, F12, F22, F91, F92
Duplex steel : F51 F60 F53 F55
Alloy Steel:4130, 4140, 4142, 4145, 4150, 4320, 4330, 4340, 4350, 4620, 4820, 6150, 8620, 8630, 8822, 9310, 52100, HY80, HY100, 9315, 300M, Nitralloy 135M, 17-22A
Aluminum : 2014, 2024, 2025, 2219, 2618, 3003, 5083, 6061, 7049, 7050, 7075, 7079, 7149, 7150, and 7175